Обогащение полезных ископаемых и руд и концентратов
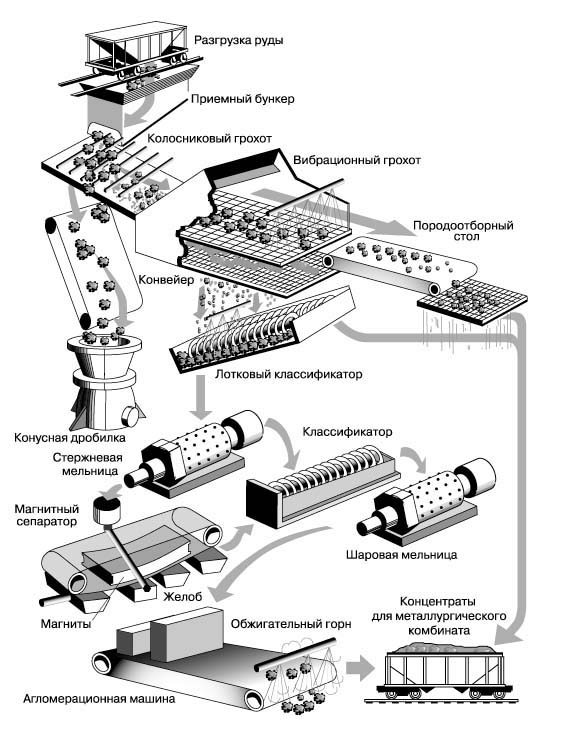
ОБОГАЩЕ́НИЕ ПОЛЕ́ЗНЫХ ИСКОПА́ЕМЫХ, совокупность процессов извлечения ценных компонентов из твёрдого минерального природного и техногенного сырья с целью получения продуктов для дальнейшей технически возможной и экономически целесообразной переработки либо использования. Способы обогащения основаны на разделении минералов по их свойствам: плотности – гравитационное обогащение; смачиваемости поверхностей – флотация; магнитной восприимчивости – магнитная сепарация; электрич. свойствам (электрич. проводимости, диэлектрич. проницаемости, способности заряжаться при трении) – электрическая сепарация; различию в естеств. и наведённой радиоактивности – радиометрическое обогащение и др. Для повышения контрастности (отличий) технологич. свойств минералов применяют разл. способы (УЗ, электрохимич., радиац., термич. и др.) воздействия на руды и продукты обогащения. О. п. и. осуществляют на обогатит. фабриках.
О. п. и. известно с древнейших времён. Первое, опубликованное в 1556, обстоятельное описание многих (естественно, примитивных) процессов обогащения дал Г. Агрикола. В России зарождение О. п. и. связано с выделением золота из руд; в 1748 на р. Исеть построена первая обогатит. фабрика для извлечения золота. В 1763 М. В. Ломоносов дал описание ряда обогатит. процессов в труде «Первые основания металлургии или рудных дел». С сер. 19 в. началось интенсивное развитие осн. механич. методов (рудоподготовка, гравитац. методы и др.), на рубеже 19–20 вв. – магнитных и электрич. методов; в 1930-х гг. получил распространение флотац. метод обогащения, который является основным при переработке руд цветных и редких металлов, горно-химич. сырья. С сер. 20 в. для переработки бедных и окисленных руд широко используются процессы выщелачивания (напр., бактериальное выщелачивание). Для руд сложного вещественного состава (в связи с вовлечением в переработку труднообогатимых руд и техногенного минер. сырья, характеризующегося низким содержанием ценных компонентов и тонкой вкрапленностью минералов) комплексное извлечение ценных компонентов достигается сочетанием обогатит. процессов с использованием гидрометаллургич., химич. и биологич. переработок (комбиниров. схемы), т. н. обогатительно-химико-металлургич. технологии (Mineral processing).
В результате О. п. и., помимо концентратов, образуются т. н. хвосты (отходы процесса обогащения с содержанием ценных компонентов значительно ниже, чем в исходном сырье), которые, в зависимости от минер. состава пород, поступают в отвал или на переработку в целях комплексного использования сырья (напр., для доизвлечения ценных компонентов) либо их применяют в качестве флюсов, строит. материалов и др. При содержании в руде нескольких полезных компонентов из неё получают селективные концентраты, содержащие преим. один ценный компонент, или комплексные концентраты (напр., медно-золотые, никель-кобальтовые), которые разделяются на ценные компоненты в металлургич. процессе. Важное значение О. п. и. определяется тем, что металлургич., химич. и др. пром. процессы основаны на переработке концентратов.
Разнообразие видов и минералого-петрографич. характеристик полезных ископаемых почти полностью исключает возможность применения однотипных схем и режимов О. п. и. В каждом конкретном случае схема О. п. и. определяется в зависимости от состава и размеров вкраплений минералов в сырье, лабораторных и полупром. исследований на обогатимость (оценка возможности и полноты извлечения, концентрации минер. компонентов).
Схема обогащения рудного сырья состоит из ряда последоват. процессов – подготовит. процессы (дробление, измельчение, грохочение и классификация сыпучих материалов), собственно обогащение и вспомогат. процессы (обезвоживание, отстаивание, фильтрование, сушка) для достижения необходимого содержания влаги в концентратах.
На обогатит. фабрике поступившая с рудника или карьера горная масса (руда, уголь) после крупного дробления (60–40 мм) подвергается рудоподготовке, которая состоит из процессов дробления (крупностью менее 30–20 мм), грохочения и классификации (усреднение материала). Дроблёный продукт может подвергаться предварит. обогащению в тяжёлых средах или методами радиометрии. Данные методы позволяют удалить до 20–50% отвального продукта (пустой породы), повысив содержание ценных компонентов в 1,5–2 раза, что обеспечивает снижение энергетич. и материальных затрат при последующих операциях обогащения. Дополнит. дробление и измельчение исходного материала проводят с целью доведения его до размеров, пригодных для проведения обогатит. процесса, а также для раскрытия руды (разделение сростков и образование частиц индивидуальных минералов). Применение центробежных и конусных инерционных дробилок позволяет снижать крупность до 10–6 мм. Тонкое измельчение (крупностью от 5 мм до 74–40 мкм) осуществляется в мельницах. Для вскрытия тонкодисперсных минер. комплексов используют разл. энергетич. методы воздействия (напр., мощные наносекундные электромагнитные импульсы), обеспечивающие высвобождение частиц до микро- и наноуровня. Измельчённый продукт подвергается обработке обогатит. методами или их комбинацией.
О. п. и. характеризуется двумя осн. показателями: содержанием в концентрате полезного компонента и его извлечением (в процентах). При О. п. и. из руд извлекают до 65–95% ценных компонентов, при этом по сравнению с рудами их концентрация возрастает в десятки и сотни раз. Эффективность О. п. и. определяется степенью раскрытия минер. комплексов (соотношения раскрытых частиц рудных и породообразующих минералов) и контрастностью технологич. свойств по разделительному признаку (удельный вес, радиоактивность, электрич., магнитные и физико-химич. свойства, цвет, форма минерала). Выбор технологии О. п. и. осуществляется с учётом требований охраны окружающей среды. В 2010 в РФ обогащению подверглось 680 млн. т разл. руд и 110 млн. т углей.
Гл. направления развития О. п. и.: создание новых экологически безопасных способов комплексного извлечения компонентов из труднообогатимого минер. сырья с применением обогатит. и химико-металлургич. процессов; разработка высокоэффективных нетрадиц. методов селективной дезинтеграции тонкодисперных минер. комплексов; совершенствование технологий переработки техногенного минер. сырья; разработка новых методов кондиционирования водной и газовой фаз.
Источник
РУДЫ ОБОГАЩЕНИЕ, методы переработки природного минерального сырья, которое представляет собой естественную смесь ценных компонентов и пустой породы, с целью получения концентратов, существенно обогащенных одним или несколькими ценными компонентами. Обогащение руды осуществляется преимущественно механическими, а также термическими и химическими методами.
Исторически обстоятельства сложились таким образом, что обогащение полезных ископаемых началось с обогащения руд; в связи с необходимостью дальнейшей переработки концентратов, полученных в результате обогащения руд, а также другого природного сырья, которое приобрело промышленную значимость, появились и другие отрасли горного дела. Первоначальные процессы обогащения руды заключались в промывке россыпных месторождений золота и дроблении крупных глыб горных пород, обогащенных самородными металлами, такими, как золото, серебро и медь. Г.Агрикола в своем труде О горном деле (De re metallica, 1556) цитирует записи, свидетельствующие о промывке россыпного золота раньше 4000 до н.э. Добыча золота из жил путем дробления и промывки производилась уже в 2400 до н.э. Сильное нагревание свинцово-серебряных руд практиковалось в Греции в 3–2 в. до н.э. Агрикола описал сложную переработку руд благородных и цветных металлов посредством методов, элементы которых включает и современная гравитационная концентрация.
К главным процессам обогащения руды относятся измельчение руды и выделение концентрата. Измельчение заключается в дроблении природного материала, обычно механическими методами, с получением смеси частиц ценных и ненужных компонентов. Дробление может также дополняться химическим разложением молекул компонентов для освобождения полезных атомов. Выделение, или концентрация, состоит в обособлении полезных частиц одного или нескольких продуктов, называемых концентратами, и исключении ненужных частиц пустой породы (хвостов, или отходов). Частицы, которые не попали ни в концентрат, ни в отходы, называются промежуточным продуктом и обычно требуют дальнейшей переработки.
Дробление.
К дроблению относятся механические процессы, посредством которых добытая в руднике порода разбивается до размеров, подходящих для дальнейшего измельчения посредством размалывания. Устройства, которые разбивают добытое в руднике сырье, относятся к первичным дробилкам; дробилки щекового и конусного типов среди них являются основными. Вторичное дробление осуществляется в один, два, реже в три этапа.
Размалывание.
Размалывание представляет собой конечный этап механического отделения полезных минералов от пустой породы. Обычно оно производится в водной среде посредством машин, в которых порода измельчается при помощи чугунных или стальных шаров, кремневой гальки, а также гальки, образующейся из твердых кусков руды или вмещающей породы.
Грохочение.
Грохочение применяется для приготовления материала определенной размерности, поступающего на концентрирование. Грохотами обычно разделяют зерна, размер которых превышает 3–5 мм; механические классификаторы используются для более тонкой сепарации мокрого материала.
Грохота.
Большинство грохотов относится к вибрационному типу. Их главным элементом является сито, пластина с отверстиями или какая-либо другая плоская перфорированная конструкция (обычно устанавливаемая наклонно под углом 20–40°), которой придается вибрация с частотой 500–3600 циклов в минуту.
Механические классификаторы.
Механические классификаторы представляют собой прямоугольные лотки с наклонным дном, которым сообщается встряхивающее и возвратно-поступательное движение. Материал, подлежащий разделению по крупности зерен, смешивается с водой, подается на верхний край классификатора и перемещается под действием силы тяжести в углубление на нижнем крае лотка. Там более тяжелые и крупные частицы оседают на дно и забираются конвейером. Более легкие и мелкие частички выносятся потоком воды.
Центробежные конусные классификаторы.
В центробежных конусных классификаторах для выделения рудных частиц используются центробежные силы в водной среде. Процесс разделения в таких классификаторах позволяет получить мелкозернистую песчано-шламовую фракцию, пригодную для дальнейшего концентрирования методом флотации.
МЕХАНИЧЕСКИЕ МЕТОДЫ ОБОГАЩЕНИЯ
Механические методы обогащения позволяют отделить ценные рудные частицы от частиц пустой породы с использованием чисто физических процессов, без химических превращений.
Гравитационная концентрация.
Гравитационная концентрация основана на использовании разной плотности различных минералов. Частицы разной плотности вводятся в жидкую среду, плотность которой имеет промежуточное значение между плотностями минералов, подлежащих разделению. Этот принцип можно проиллюстрировать отделением песка от опилок, когда их бросают в воду; опилки всплывают, а песок тонет в воде.
Обогащение в тяжелой среде.
Метод обогащения в тяжелой среде основан на использовании суспензии, состоящей, помимо частиц руды, из воды и твердого компонента. Плотность суспензии варьируется от 2,5 до 3,5 в зависимости от свойств разделяемых минералов. При этом используются конические или пирамидальные емкости.
Отсадочные машины.
Отсадочная машина – это один из видов гравитационного концентратора, в котором суспензия состоит из воды и рудных частиц.
В отсадочных машинах непрерывного действия имеются по крайней мере два отделения. Тяжелые частицы, попавшие в приемное отделение, скапливаются на дне; более легкие частицы всплывают. Подаваемый материал захватывается текущей водой и поступает в поверхностный слой на нижней части уклона, который стремится выплеснуться через край. Однако тяжелый материал проседает через более легкий и оказывается в придонном слое. Легкий материал смешивается с верхним слоем, и поперечный поток воды сносит его через перегородку в соседнее отделение, где происходит аналогичная сепарация. Автоматические разгрузочные устройства удаляют придонный слой с такой скоростью, чтобы он сохранял необходимую толщину.
Концентрационные столы.
Концентрационные столы представляют собой гравитационные концентраторы, приспособленные для переработки материала песчаной фракции с размером зерна менее 2,5 мм. Главный их элемент – это покрытая линолеумом прямоугольная дека шириной 1,2–1,5 м и длиной около 4,8 м. Она устанавливается с небольшим регулируемым поперечным уклоном и испытывает возвратно-поступательное движение вдоль длинной стороны с частотой 175–300 циклов в минуту и амплитудой от 6 до 25 мм.
Дека имеет рифленую поверхность; при этом высота ее гребней уменьшается в направлении диагонали деки от края стола, где производится подача материала, к его выгрузочному концу. Водная суспензия попадает в бороздки и там расслаивается: более тяжелый материал оседает на дно, а более легкий оказывается наверху. Под воздействием возвратно-поступательного движения легкий материал передвигается по деке. Поскольку высота гребней к выгрузочному концу стола уменьшается, верхний слой смывается потоком воды, идущим поперек стола, и уносится вниз к его боковой стороне, тогда как более тяжелый материал переносится к выгрузочному концу.
Шлюзы.
Концентрационный шлюз представляет собой наклонный желоб с шероховатым дном, вдоль которого перемещается гравий россыпи (золотоносной или оловоносной), увлекаемый потоком воды; при этом тяжелые минералы оседают на дне углублений и удерживаются там, тогда как легкие выносятся. Шероховатость дна создается деревянными брусками, рейками, рифленой резиной, небольшими жердями и даже железнодорожными рельсами, устанавливаемыми вдоль или поперек желоба. Для переработки мелкозернистого песка и шлама дно шлюза покрывают мешковиной, брезентом или другим подобным материалом, который обычно прикрепляется металлической решеткой или грубой проволочной сеткой. При переработке золотоносного гравия для сепарации довольно часто используется ртуть благодаря ее способности прилипать к мелким частичкам золота и удерживать их в потоке воды. Ширина шлюза составляет от 0,5 до 2 м, а длина – от 3–6 м до 1,5 км и более. Наклон варьируют в пределах 2,0–12,5 см/м; при этом в нижней части шлюза преобладает тонкозернистый материал с большим количеством воды, а в верхней части – более грубозернистый с меньшим количеством воды. Периодически подачу материала прекращают и создают легкий поток воды, рифли снимают, начиная с выходного конца, осевший песок переворачивают лопатами для отмывки легкого песка, а оставшуюся часть сгребают в бадьи. Очищенный золотоносный продукт затем обрабатывается в промывочном лотке (диаметром 0,45 м и глубиной 5–8 см) с наклонными под углом 45° стенками. Когда песок вместе с водой в лотке встряхивается, тяжелый материал оседает, а легкие отходы смываются через край.
Флотация.
Флотация основана на различиях физико-химических свойств поверхности минералов в зависимости от их состава, что вызывает селективное прилипание частиц к пузырькам воздуха в воде. Агрегаты, состоящие из пузырьков и прилипших частичек, всплывают на поверхность воды, тогда как не прилипшие к пузырькам частицы оседают, в результате чего происходит разделение минералов.
Прилипание к пузырькам усиливается при селективном покрытии частиц одного из минералов поверхностно-активным веществом. Примером такого вещества может служить парафин. Погрузите покрытую парафином частицу в газированную воду, и пузырьки выделившегося углекислого газа прилипнут к нему. Если частица достаточно маленькая, то она всплывет. Углеводородные ионы, в которых химически активная группа представлена производными тиокислот (ксантогенаты, тиофосфаты, меркаптаны и подобные им соединения), взаимодействуют предпочтительно с ионами тяжелых металлов.
Флотация обеспечивает получение высокосортных концентратов. При этом флотационные реагенты составляют главную статью расходов. Этот процесс позволяет разделить практически любые два минерала, которые содержат существенно разные химические элементы или ионные группы.
Электрическая и магнитная сепарация.
Сепарация такого рода основана на различной поверхностной проводимости или магнитной восприимчивости разных минералов.
Магнитная сепарация.
Магнитная сепарация применяется для обогащения руд, содержащих минералы с относительно высокой магнитной восприимчивостью. К ним относятся магнетит, франклинит, ильменит и пирротин, а также некоторые другие минералы железа, поверхности которых могут быть приданы нужные свойства путем низкотемпературного обжига. Сепарация производится как в водной, так и в сухой среде. Сухая сепарация больше подходит для крупных зерен, мокрая – для тонкозернистых песков и шламов. Обычный магнитный сепаратор представляет собой устройство, в котором слой руды толщиной в несколько зерен перемещается непрерывно в магнитном поле. Магнитные частицы вытягиваются из потока зерен лентой и собираются для дальнейшей переработки; немагнитные частицы остаются в потоке.
Электростатическая сепарация.
Электростатическая сепарация основана на различной способности минералов пропускать электроны по своей поверхности, когда они находятся под поляризующим воздействием электрического поля. В результате частицы разного состава заряжаются в разной степени при определенных значениях напряженности этого поля и времени его воздействия и, как следствие, по разному реагируют на одновременно действующие на них электрические и другие силы, обычно гравитационные. Если таким заряженным частицам предоставить возможность свободно перемещаться, то направления их движения будут различаться, что и используется для разделения.
ХИМИЧЕСКИЕ МЕТОДЫ ОБОГАЩЕНИЯ
Химические методы обогащения включают, в качестве предварительного этапа, измельчение руды, которое открывает доступ химическим реагентам к ценным компонентам руды, после чего облегчается извлечение этих компонентов. Химические методы могут быть применены как непосредственно к рудам, так и к концентратам, полученным в результате обогащения руд механическими методами. Терминология методов химического обогащения до некоторой степени запутана. В рамках этой статьи разделение в расплаве относится к процессу плавления, а разделение путем селективных химических реакций – к процессу выщелачивания.
Плавление.
Плавление – это химический процесс, происходящий при высоких температурах, в ходе которого ценный металл и пустая порода переходят в расплавленное состояние. Поскольку металл имеет более высокую плотность и нерастворим в расплавленной пустой породе, он отделяется от последней и погружается на дно. Метод плавления имеет свои специфические особенности для каждого металла. Например, свинцовый концентрат смешивается с твердыми реагентами в определенных соотношениях, чтобы получить загрузку печи такого состава, которая при нагревании до достаточно высоких температур приводит к образованию за счет пустой породы сложных силикатов (шлака), остающихся на поверхности расплавленного металлического свинца. При выпускании металла со дна печи получается черновой свинец. При наличии в свинцовом концентрате меди образуются три слоя: нижний слой свинца, средний слой сульфида меди (штейн) и верхний слой шлака. Они выпускаются из печи раздельно. Штейн затем перерабатывается в другой печи (конвертере), через которую продувают воздух для удаления серы, получая в результате черновую (пористую) медь.
Обжиг.
Обжиг в ходе подготовки к выщелачиванию применяется либо для изменения химического состава полезных составляющих, что делает их пригодными для выщелачивания, либо для удаления некоторых примесей, присутствие которых значительно затрудняет и удорожает процесс выщелачивания ценных компонентов. Например, некоторые руды золота, содержащие мышьяк и серу, перед выщелачиванием подвергают обжигу для удаления этих составляющих.
Выщелачивание.
При выщелачивании ценные компоненты руды растворяются и отделяются от нерастворимого остатка посредством подходящего растворителя. В некоторых случаях для перевода ценного компонента в растворимую форму добавляется реагент. Эффективность (скорость и полнота протекания) процесса зависит от размера частиц, свойств реагентов, применяемых для выщелачивания, температуры и метода приведения в соприкосновение руды с растворителем или реагентами. Обычно чем меньше размер частиц, выше температура и концентрация выщелачивающих химических соединений, тем быстрее идет процесс.
Методы непосредственного воздействия на руду выщелачивающих растворов.
К этим методам относятся кучное выщелачивание, выщелачивание при просачивании и выщелачивание при перемешивании. Эти методы могут применяться как в периодических, так и в непрерывных процессах. В свою очередь непрерывные процессы могут быть реализованы как прямоточные либо как противоточные. В прямоточном процессе выщелачивающий раствор движется вместе с рудой и пополняется по мере его истощения. В противоточном процессе выщелачивающий раствор движется навстречу потоку руды. При этом передовой фронт раствора, встречаемый свежей порцией руды, обеднен реагентами и насыщен экстрагированным материалом, а тыловые порции раствора, которые позже встречаются с рудой, представлены свежим выщелачивающим раствором.
Кучное выщелачивание применяется для переработки руд, содержащих легко растворимые полезные компоненты; такие руды должны быть относительно пористыми и недорогими (обычно они добываются в открытых разработках). Иногда кучное выщелачивание используется для переработки отвалов, возникших в результате процессов предшествующей добычи и утилизации руды, когда затраты на добычу уже произведены. Для загрузки руды подготавливается слабо наклонная поверхность, непроницаемая для выщелачивающих растворов. Вдоль и поперек этой поверхности создаются водосборные углубления для дренажа. После загрузки руда заливается большим количеством выщелачивающего раствора, достаточным для того, чтобы пропитать всю ее толщу. Раствор проникает между частицами руды и производит растворение полезных компонентов. Через некоторый период времени материал высушивают и извлекают корку, образованную растворившимися ценными составляющими, а обработанную рыхлую породу смывают в дренажную систему.
Выщелачивание путем просачивания используется при переработке руд, которые при дроблении измельчаются плохо и не содержат природного шлама или глины. Это довольно медленный процесс. Выщелачивание при просачивании осуществляется главным образом в баках, хорошо приспособленных для загрузки и разгрузки. Дно бака должно быть эффективным фильтром, позволяющим производить через него закачку и откачку раствора. Баки загружаются раздробленной рудой определенной фракции крупности; иногда в целях более плотной и равномерной загрузки она смачивается. Затем выщелачивающий раствор закачивается в бак и впитывается в руду. По истечении необходимого времени выдержки раствор с выщелоченными компонентами откачивается, а руда промывается для удаления остатков выщелачивающего раствора.
Выщелачивание с перемешиванием обычно применяется при переработке высокосортных руд или концентратов с относительно небольшим объемом материала, подлежащего выщелачиванию, а также руд, содержащих тонкую рассеянную вкрапленность полезных компонентов либо измельченных до весьма мелкозернистой фракции. Выщелачивание с перемешиванием позволяет сократить время взаимодействия растворов с рудой до нескольких часов по сравнению с сутками, которые требуются для выщелачивания при просачивании.
Извлечение ценных компонентов.
Извлечение ценных компонентов из растворов после выщелачивания, содержащих растворенные полезные составляющие, может осуществляться путем химического осаждения, экстракции растворителем, ионообменным методом или электролизом.
Для химического осаждения раствор после выщелачивания подвергается воздействию соответствующих химических реагентов, в результате чего ценные компоненты переходят в форму нерастворимых соединений, которые выпадают в осадок, а затем отделяются путем отсадки или фильтрования.
Экстракция растворителем представляет собой сравнительно новый метод, предложенный для переработки урановых руд. Раствор, содержащий выщелоченные ценные компоненты (называемый водной фазой), взаимодействует с несмешивающимся органическим растворителем (называемым органической фазой), в результате чего полезная составляющая переходит из водной фазы в органическую. Затем органическая фаза, несущая ценные компоненты, отделяется и взаимодействует с другой водной фазой, куда компоненты и переходят; этот процесс называется десорбированием. Новая водная фаза с извлеченными ценными компонентами обрабатывается с целью их осаждения. Органической фазой служит какой-либо органический растворитель, например, трибутилфосфат, а в качестве разбавителя обычно используется керосин.
Ионообменный процесс извлечения из руды ценных компонентов разработан сравнительно недавно. Он основан на том явлении, что синтетические смолы могут селективно экстрагировать нужные компоненты из содержащих их растворов. Ионообменные смолы синтезируются путем полимеризации с отщеплением воды. После полимеризации в смоле возникают функциональные группы, например, карбоксиловая (– COONa), сульфониловая (– SO3Na) или аминовая (– NH2ЧHCl). Первые два примера соответствуют катионообменной смоле, ион натрия (Na+1) которой обменивается на положительно заряженный ион, содержащий ценный компонент; отрицательно заряженный ион хлора (Cl–1) анионообменной смолы с аминовой группой обменивается на отрицательно заряженный ион, содержащий ценный компонент.
Источник